Przewody spawalnicze – zawarte tajemnice wyboru idealnych do twojego przemysłu
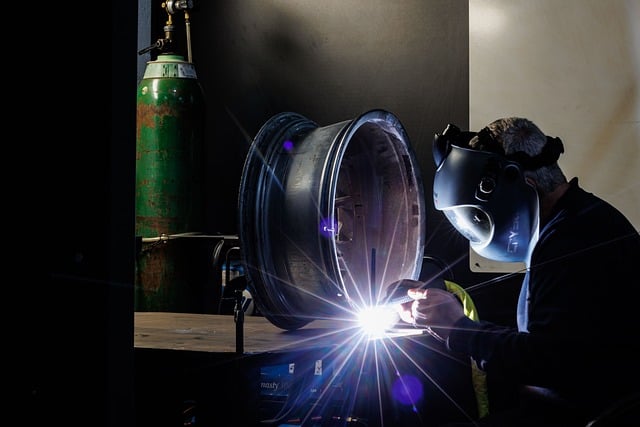
W świecie konstrukcji metalowych, gdzie precyzja łączenia elementów gra kluczową rolę, odpowiedni wybór przewodów spawalniczych może stanowić różnicę między sukcesem a porażką projektu. Każdy szczegół ma znaczenie, a zaklęte w metalowych żyłach tajemnice mogą wyznaczać ścieżkę do wydajności i trwałości. Czy jesteś gotów odkryć, które przewody spawalnicze okażą się idealne dla Twojego przemysłu? Zapraszamy do zgłębienia tematu, który może zaważyć na jakości Twoich prac spawalniczych.
Różne typy przewodów spawalniczych i ich zastosowania
Pierwszym z różnych typów przewodów spawalniczych, które warto omówić, są przewody MIG (Metal Inert Gas). Są one głównie używane w przemyśle motoryzacyjnym i stoczniowym, oferując wysoką wydajność oraz precyzyjność. Przewód spawalniczy typu MIG jest idealny do pracy na różnych materiałach, w tym na stali, stali nierdzewnej i aluminium.
Kolejnym typem są przewody TIG (Tungsten Inert Gas), które są znane ze swojej wyjątkowej precyzji i czystości spoin. Często stosowane w przemyśle lotniczym, kosmicznym oraz w produkcji sprzętu medycznego, przewody TIG są doskonałe do spawania cienkich blach i rur. Dzięki temu procesowi powstają łączenia o wysokiej jakości, odporne na korozję oraz działanie wysokich temperatur.
Przewody spawalnicze typu flux-cored (z rdzeniem proszkowym) to kolejny typ, który zasługuje na uwagę. Są one często wykorzystywane w budownictwie, przemyśle ciężkim oraz w produkcji sprzętu rolniczego. Stosowanie tych przewodów pozwala na efektywne spawanie w trudnych warunkach, takich jak na zewnątrz, w silnym wietrze.
Na koniec warto wspomnieć o przewodach spawalniczych typu stick (elektroda otulona). Znane z swojej uniwersalności, są one często wykorzystywane w różnych gałęziach przemysłu, w tym w budownictwie, produkcji i naprawie sprzętu ciężkiego oraz w przemyśle stoczniowym. Przewody stick są niezwykle wydajne w spawaniu grubych materiałów i prac w trudno dostępnych miejscach.
Kluczowe czynniki do uwzględnienia przy wyborze przewodów spawalniczych
Podczas wyboru przewodów spawalniczych, kluczowe jest zrozumienie specyfiki danej operacji spawalniczej. Czy jest to praca na otwartym powietrzu, czy w kontrolowanych warunkach fabrycznych? Czy materiał, który ma być spawany, jest gruby czy cienki? Odpowiedzi na te pytania pomogą Ci wybrać odpowiedni typ przewodu spawalniczego dla Twojego przemysłu.
Materiał, z którego wykonane są przewody spawalnicze, ma ogromne znaczenie dla jakości wykonanej spoiny. Stal, stal nierdzewna, aluminium, czy inne materiały, mają swoje specyficzne właściwości, które wpływają na proces spawania. Wybór odpowiedniego przewodu spawalniczego powinien zatem być uzależniony od rodzaju materiału, który ma być złączony.
Na koniec, niezwykle istotny jest również wymiar przewodów spawalniczych. Grubość przewodu wpływa na moc i temperaturę procesu spawania. Przewody o większym przekroju są idealne do spawania grubych materiałów, podczas gdy cieńsze przewody są doskonałe do precyzyjnego spawania cienkich blach i rur.
Jak dobór przewodów wpływa na efektywność procesu spawania
Wybór odpowiednich przewodów spawalniczych jest kluczowy dla efektywności całego procesu spawania. Ta zależność wynika z faktu, że różne typy przewodów są przeznaczone do różnych zastosowań i posiadają unikalne właściwości, które wpływają na jakość spoiny, szybkość pracy i ogólną wydajność procesu spawania.
Na przykład, przewody MIG są idealne do pracy ze stalą, oferując wysoką wydajność i precyzję, podczas gdy przewody TIG są doskonałe do spawania cienkich blach i rur, zapewniając wyjątkową precyzję i czystość spoin. Wybór niewłaściwych przewodów może prowadzić do niskiej jakości łączeń, niewystarczającej wydajności, a w efekcie do zwiększenia kosztów produkcji.
Podobnie, wymiary przewodów spawalniczych mają bezpośredni wpływ na moc i temperaturę procesu spawania. Przewody o większym przekroju są idealne do spawania grubych materiałów, podczas gdy cieńsze przewody są doskonałe do precyzyjnego spawania cienkich blach. W ten sposób, dobór przewodów wpływa nie tylko na jakość wykonanej spoiny, ale także na efektywność i ekonomiczność całego procesu spawania.
Przykładowe sytuacje, w których dobór przewodów spawalniczych miał kluczowe znaczenie
W przemyśle stoczniowym, gdzie grubość blach i wymogi normatywne są niezwykle rygorystyczne, dobór odpowiednich przewodów spawalniczych ma kluczowe znaczenie przy budowie kadłubów statków. Użycie przewodów o zbyt małej grubości lub niewłaściwych właściwościach mogłoby mieć fatalne skutki dla wytrzymałości i bezpieczeństwa konstrukcji.
W produkcji elementów lotniczych, gdzie każdy gram ma znaczenie, wybór lekkich i zarazem wytrzymałych przewodów spawalniczych pozwala na osiągnięcie optymalnej wydajności i bezpieczeństwa samolotów. Zastosowanie przewodów TIG umożliwia precyzyjne łączenie delikatnych komponentów, które mają bezpośredni wpływ na funkcjonowanie maszyn latających.
Podczas modernizacji instalacji przemysłowych, gdzie wymagana jest szybkość działania i minimalizacja przestojów, przewody spawalnicze flux-cored okazują się niezawodne. Dzięki ich użyciu, możliwe jest efektywne spawanie w trudnych warunkach, co przyspiesza proces modernizacji i minimalizuje koszty związane z przestojami w produkcji.
W przemyśle samochodowym, podczas spawania komponentów narażonych na wysokie temperatury, jak na przykład kolektory wydechowe, dobór właściwych przewodów spawalniczych typu MIG wpływa na trwałość i wytrzymałość spoin. To przyczynia się do wydłużenia żywotności pojazdów oraz zwiększenia satysfakcji wśród użytkowników.
Najczęściej popełniane błędy przy wyborze przewodów spawalniczych i jak ich unikać
Nieodpowiednie dopasowanie przewodu do materiału spawanego jest jednym z najczęściej popełnianych błędów. Przy wyborze przewodów spawalniczych, należy dokładnie analizować rodzaj i grubość materiału bazowego. Stosowanie przewodu przeznaczonego do cienkich blach na grubych elementach może skutkować niewystarczającą penetracją i słabymi łączeniami.
Drugim błędem jest niedocenianie wpływu warunków zewnętrznych na wybór przewodów. Przewody flux-cored są doskonałe do pracy na zewnątrz, jednak ich zastosowanie w kontrolowanym środowisku warsztatowym może generować nadmierny koszt. Zawsze należy dostosować typ przewodu do specyfiki środowiska pracy, aby zapewnić optymalną wydajność i jakość spoin.
Nieprawidłowe dopasowanie średnicy przewodu jest kolejną pułapką. Zbyt gruby przewód może powodować problemy z podawaniem, a zbyt cienki – nadmierne spalanie elektrody. Kluczowe jest, aby średnicę przewodu dopasować nie tylko do grubości materiału, ale również do możliwości sprzętu spawalniczego.
Ostatnim błędem jest ignorowanie specyfikacji technicznych i zaleceń producenta sprzętu spawalniczego. Zaniedbanie takich informacji może prowadzić do nieprawidłowego doboru przewodów spawalniczych, co z kolei negatywnie wpłynie na cały proces spawania. Zawsze warto konsultować się z dokumentacją techniczną i ekspertami, aby wybrać idealnie dopasowane rozwiązania.
Podsumowanie
Wybór idealnych przewodów spawalniczych to nie tylko kwestia techniczna, ale również sztuka, która wymaga wiedzy i doświadczenia. Pamiętaj, że każdy detal ma znaczenie dla efektywności i trwałości Twoich prac spawalniczych. Niezależnie od tego, czy działasz w przemyśle stoczniowym, lotniczym, motoryzacyjnym czy budowlanym, odpowiednio dobrane przewody spawalnicze mogą znacząco wpłynąć na sukces Twoich projektów. Zachęcamy Cię do dalszego zgłębiania tajników tej fascynującej dziedziny, aby odkryć przewody idealnie odpowiadające potrzebom Twojego przemysłu i przyczynić się do podnoszenia standardów jakościowych w branży spawalniczej.