Jak wybrać i efektywnie wykorzystać kamerę termowizyjną w branży elektryczno-hydraulicznej
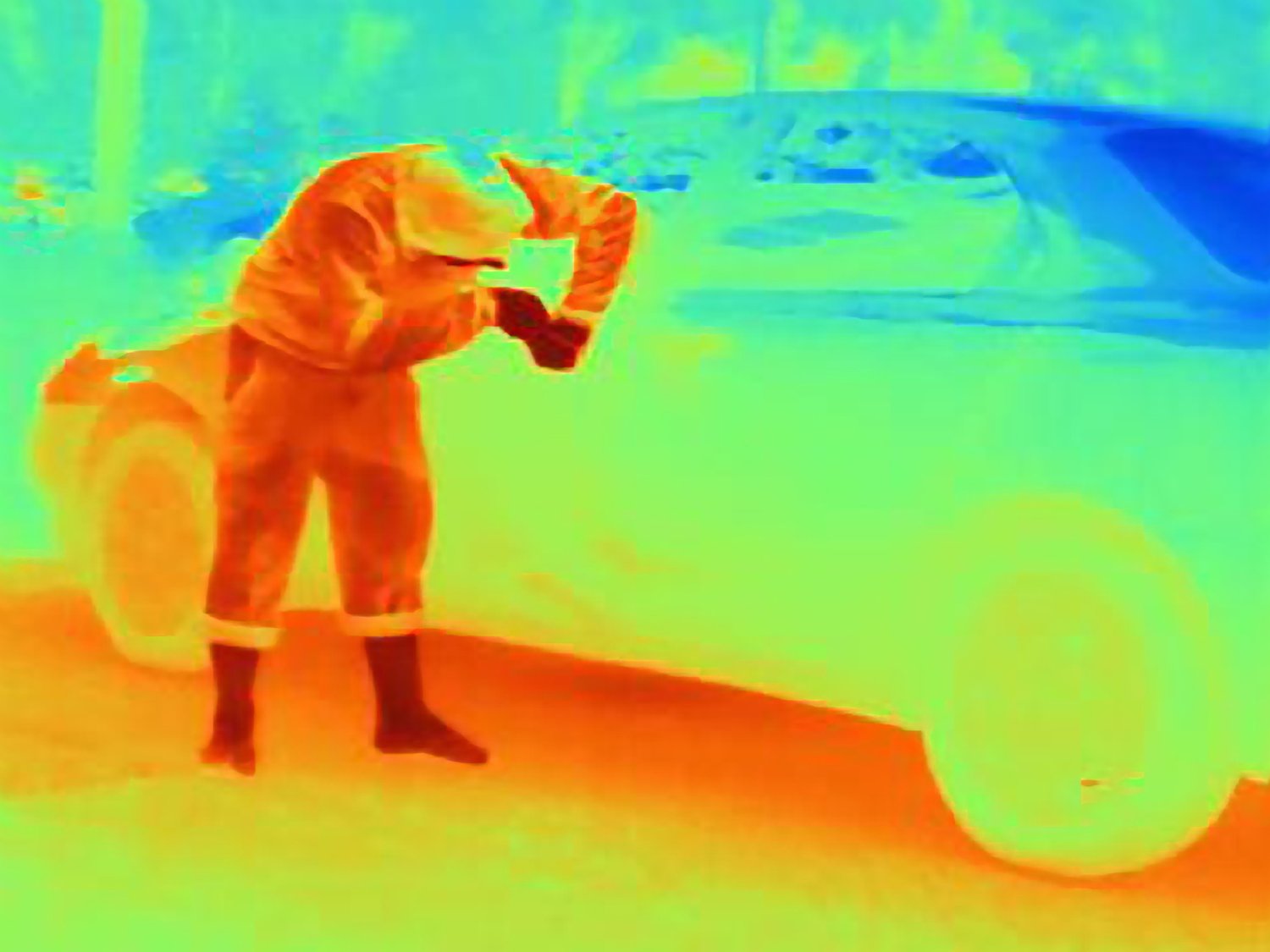
Podstawy działania kamer termowizyjnych
Kamera termowizyjna to zaawansowane urządzenie pomiarowe wykorzystywane w wielu branżach. Działa ona na zasadzie detekcji promieniowania podczerwonego emitowanego przez obiekty. Urządzenie to przekształca niewidoczne dla ludzkiego oka promieniowanie cieplne na obraz widzialny. Każdy piksel takiego obrazu reprezentuje temperaturę danego punktu. Dzięki temu możliwe jest precyzyjne mapowanie rozkładu temperatur na badanej powierzchni.
Nowoczesne kamery termowizyjne oferują rozdzielczość od 160×120 do nawet 640×480 pikseli. Wyższa rozdzielczość przekłada się na dokładniejszy obraz termiczny. Czułość temperaturowa tych urządzeń sięga często 0,05°C. Pozwala to na wykrycie nawet niewielkich różnic temperatur. Zakres pomiarowy typowej kamery termowizyjnej to zazwyczaj od -20°C do +650°C.
Kluczowym parametrem jest emisyjność, czyli zdolność powierzchni do emitowania promieniowania podczerwonego. Dla uzyskania wiarygodnych wyników pomiaru konieczne jest jej prawidłowe ustawienie. Wartość emisyjności zależy od rodzaju materiału i stanu jego powierzchni. Dla większości niemetali wynosi ona około 0,95.
Kamery termowizyjne znajdują szerokie zastosowanie w diagnostyce instalacji elektrycznych i hydraulicznych. Umożliwiają bezkontaktowy pomiar temperatury, co jest szczególnie istotne przy badaniu elementów pod napięciem. Dzięki nim można szybko zlokalizować przegrzane połączenia, uszkodzone izolacje czy nieszczelności w rurociągach.
Wybór odpowiedniej kamery termowizyjnej
Przy wyborze kamery termowizyjnej należy uwzględnić kilka kluczowych parametrów. Rozdzielczość detektora ma zasadniczy wpływ na jakość obrazu termicznego. Dla zastosowań w branży elektryczno-hydraulicznej zaleca się rozdzielczość minimum 160×120 pikseli. Czułość temperaturowa na poziomie 0,1°C lub lepsza zapewni wykrycie nawet niewielkich anomalii temperaturowych.
Zakres pomiarowy powinien być dostosowany do specyfiki wykonywanych pomiarów. Dla większości zastosowań wystarczający będzie zakres od -20°C do +350°C. Ważną cechą jest także pole widzenia obiektywu. Szerszy kąt widzenia ułatwia inspekcję dużych powierzchni, podczas gdy węższy umożliwia bardziej precyzyjne pomiary z większej odległości.
Istotną rolę odgrywa również ergonomia urządzenia. Lekka i poręczna konstrukcja ułatwia długotrwałą pracę. Duży i czytelny wyświetlacz pozwala na wygodną analizę obrazów termicznych bezpośrednio w terenie. Warto zwrócić uwagę na intuicyjność obsługi i dostępne funkcje analityczne.
Na rynku dostępne są urządzenia pomiarowe różnych producentów. Wśród najbardziej popularnych marek można wymienić Fluke, FLIR czy Sonel. Każda z nich oferuje szeroki wybór modeli o zróżnicowanych parametrach i funkcjonalnościach. Wybór konkretnego urządzenia powinien być podyktowany indywidualnymi potrzebami i specyfiką wykonywanych zadań.
Zastosowania kamer termowizyjnych w branży elektryczno-hydraulicznej
Kamera termowizyjna Sonel znajduje szerokie zastosowanie w diagnostyce instalacji elektrycznych. Umożliwia wykrywanie przegrzanych połączeń, przeciążonych obwodów czy uszkodzonych bezpieczników. Inspekcja rozdzielnic elektrycznych za pomocą kamery termowizyjnej pozwala na szybkie zlokalizowanie potencjalnych źródeł awarii. W przypadku silników elektrycznych kamera pomoże zidentyfikować problemy z łożyskami czy przegrzewające się uzwojenia.
W hydraulice kamery termowizyjne sprawdzają się przy lokalizacji wycieków i nieszczelności. Umożliwiają wykrycie zatorów w rurociągach czy nieprawidłowo działających zaworów. Szczególnie przydatne są przy diagnostyce ogrzewania podłogowego, gdzie pozwalają na precyzyjne zlokalizowanie uszkodzonych odcinków instalacji. Kamery termowizyjne znajdują również zastosowanie w ocenie skuteczności izolacji termicznej budynków.
Wykorzystanie kamer termowizyjnych znacząco przyspiesza proces diagnostyczny. Eliminuje konieczność demontażu elementów instalacji w celu lokalizacji usterki. Pozwala na wykrycie problemów na wczesnym etapie, zanim doprowadzą one do poważnej awarii. Regularne inspekcje termowizyjne stanowią element prewencyjnego utrzymania ruchu, przyczyniając się do zwiększenia niezawodności instalacji.
Warto zaznaczyć, że interpretacja obrazów termicznych wymaga odpowiedniej wiedzy i doświadczenia. Konieczne jest uwzględnienie warunków otoczenia i specyfiki badanych obiektów. Dlatego też zaleca się, aby pomiary termowizyjne były wykonywane przez przeszkolony personel.
Praktyczne wskazówki dotyczące pomiarów termowizyjnych
Przed przystąpieniem do pomiarów termowizyjnych należy odpowiednio przygotować kamerę. Kluczowe jest prawidłowe ustawienie emisyjności dla badanego obiektu. Dla większości materiałów budowlanych i elementów instalacji elektrycznych można przyjąć wartość 0,95. W przypadku powierzchni metalowych konieczne może być wykorzystanie specjalnych naklejek o znanej emisyjności.
Ważne jest uwzględnienie wpływu warunków otoczenia na wyniki pomiarów. Temperatura i wilgotność powietrza mogą znacząco wpływać na odczyty. Należy unikać wykonywania pomiarów w bezpośrednim nasłonecznieniu czy przy silnym wietrze. Optymalne warunki to stabilna temperatura otoczenia i brak opadów atmosferycznych.
Kamera termowizyjna Fluke i inne profesjonalne modele oferują funkcję automatycznego łączenia obrazu termicznego z obrazem w świetle widzialnym. Ułatwia to późniejszą analizę i interpretację wyników. Podczas wykonywania zdjęć należy zadbać o odpowiedni kąt i odległość od badanego obiektu. Unikać należy odbić i refleksów, które mogą zniekształcić obraz termiczny.
Po wykonaniu pomiarów konieczna jest dokładna analiza uzyskanych obrazów. Większość kamer termowizyjnych umożliwia podstawową obróbkę bezpośrednio na urządzeniu. Dla bardziej zaawansowanych analiz wykorzystuje się dedykowane oprogramowanie komputerowe. Pozwala ono na precyzyjne pomiary temperatury w wybranych punktach, tworzenie profili temperaturowych czy generowanie raportów.