Modernizacja systemów automatyki przemysłowej z wykorzystaniem sterowników programowalnych
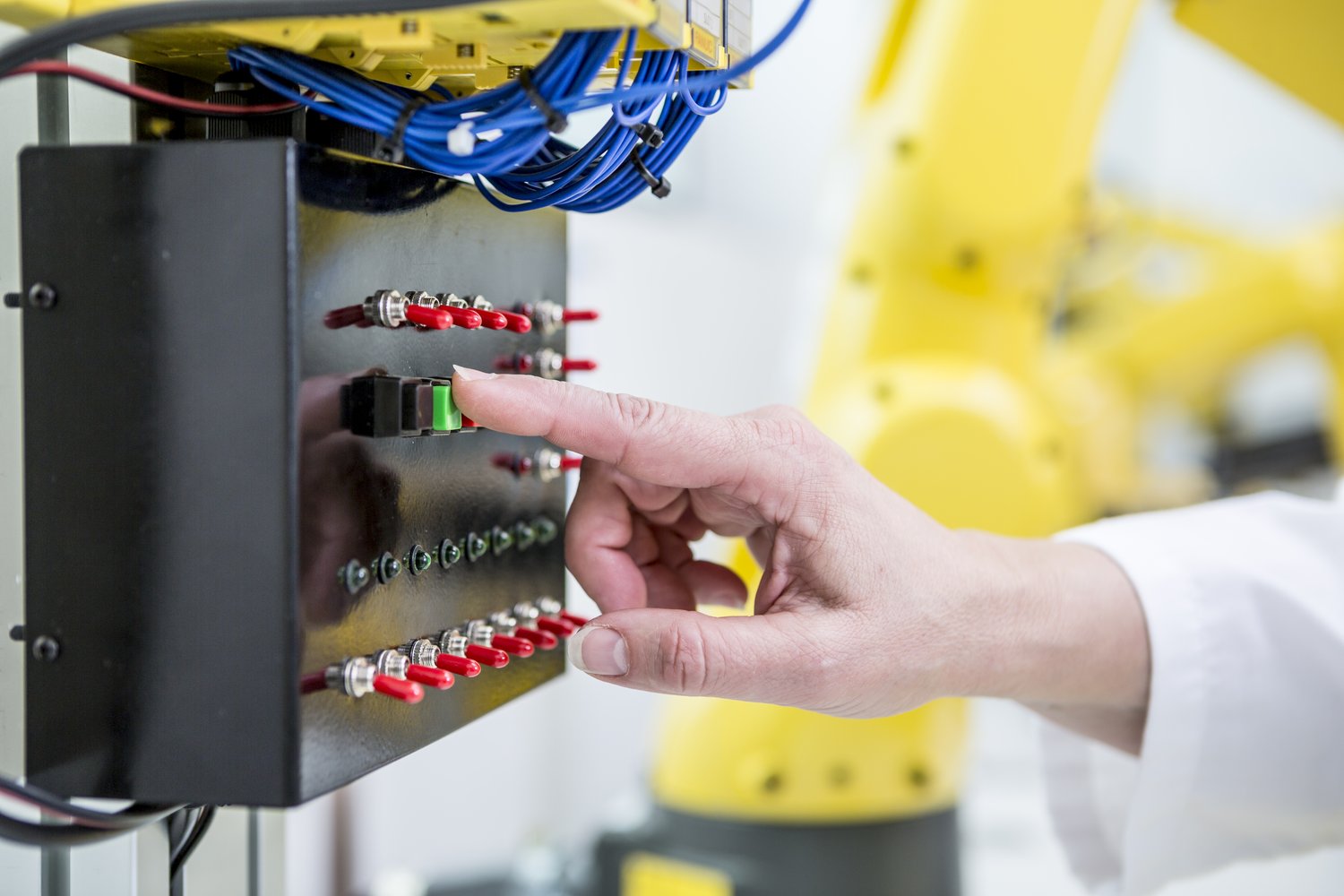
Podstawy automatyki przemysłowej
Automatyka odgrywa kluczową rolę w przemyśle i utrzymaniu ruchu. Systemy automatyki kontrolują procesy produkcyjne, zwiększając ich efektywność i bezpieczeństwo. W nowoczesnych fabrykach znajduje się wiele urządzeń automatyki, takich jak czujniki, siłowniki czy sterowniki. Ich zadaniem jest monitorowanie parametrów procesu i sterowanie maszynami. Automatyzacja pozwala zredukować koszty produkcji nawet o 30%. Wdrożenie systemów automatyki wymaga jednak specjalistycznej wiedzy i doświadczenia.
Sercem systemów automatyki są sterowniki programowalne. Urządzenia te przetwarzają sygnały z czujników i sterują elementami wykonawczymi. Typowy sterownik posiada od kilku do kilkudziesięciu wejść i wyjść. Jego program można modyfikować w zależności od potrzeb. Sterowniki programowalne stosuje się w liniach produkcyjnych, maszynach, systemach budynkowych. Ich wykorzystanie zwiększa elastyczność procesów i ułatwia diagnostykę. Nowoczesne sterowniki oferują zaawansowane funkcje, jak komunikacja sieciowa czy wizualizacja procesu.
Wybór odpowiedniego sterownika zależy od wielu czynników. Należy uwzględnić liczbę wymaganych wejść/wyjść, złożoność procesu, warunki środowiskowe. Istotna jest też możliwość rozbudowy systemu w przyszłości. Popularne marki sterowników to Siemens, Allen-Bradley, Mitsubishi. Dla prostszych aplikacji sprawdzą się ekonomiczne sterowniki, jak sterownik programowalny F&F. Oferują one dobre możliwości w przystępnej cenie. Przy wyborze warto skonsultować się ze specjalistą automatyki.
Programowanie sterowników wymaga specjalistycznych narzędzi i umiejętności. Wykorzystuje się do tego dedykowane środowiska programistyczne. Najpopularniejsze języki to drabinkowy, FBD czy ST. Program sterownika składa się z bloków funkcyjnych realizujących określone zadania. Jego struktura powinna być przejrzysta i dobrze udokumentowana. Ważne jest też uwzględnienie zabezpieczeń i obsługi sytuacji awaryjnych. Prawidłowo zaprogramowany sterownik zapewnia niezawodne działanie systemu automatyki.
Projektowanie systemów sterowania
Proces projektowania systemu sterowania zaczyna się od analizy wymagań. Należy dokładnie określić funkcje, jakie ma realizować automatyka. Ważne jest też zdefiniowanie parametrów procesu i warunków pracy. Na tej podstawie dobiera się odpowiednie komponenty systemu. Kluczowy jest wybór sterownika o odpowiedniej mocy obliczeniowej i liczbie wejść/wyjść. Projektant musi też uwzględnić interfejsy komunikacyjne i protokoły. Dobrze zaprojektowany system powinien być skalowalny i łatwy w utrzymaniu.
Kolejnym etapem jest opracowanie algorytmów sterowania. Określają one logikę działania systemu w różnych sytuacjach. Algorytmy uwzględniają sekwencje operacji, warunki przejść między stanami, obsługę alarmów. Ich implementacja w sterowniku wymaga znajomości języków programowania PLC. Typowy program sterownika składa się z kilkudziesięciu do kilkuset bloków funkcyjnych. Istotne jest optymalne wykorzystanie zasobów sterownika i zapewnienie determinizmu czasowego.
Ważnym elementem projektu jest interfejs operatorski HMI. Umożliwia on wizualizację procesu i zadawanie parametrów. Dobrze zaprojektowany HMI zwiększa ergonomię pracy operatorów. Powinien prezentować kluczowe informacje w przejrzysty sposób. Nowoczesne systemy HMI oferują zaawansowane funkcje, jak trendy historyczne czy raporty. Ich integracja ze sterownikiem wymaga konfiguracji protokołów komunikacyjnych. Projektant musi zadbać o intuicyjną nawigację i czytelne oznaczenia elementów graficznych.
Ostatnim etapem jest przygotowanie dokumentacji technicznej. Obejmuje ona schematy elektryczne, listę sygnałów, opis algorytmów. Ważną częścią jest instrukcja obsługi systemu dla operatorów. Dokumentacja powinna być kompletna i aktualna. Ułatwia to późniejsze modyfikacje i serwis systemu. Dobra dokumentacja to podstawa sprawnego utrzymania ruchu. Jej przygotowanie wymaga jednak czasu – zwykle stanowi 20-30% nakładu pracy przy projekcie.
Wdrażanie i utrzymanie systemów automatyki
Przemysł i utrzymanie ruchu stawiają wysokie wymagania przed systemami automatyki. Ich wdrożenie musi być dobrze zaplanowane i przeprowadzone. Zwykle zaczyna się od testów na stanowisku próbnym. Pozwala to wykryć ewentualne błędy w oprogramowaniu. Następnie system jest instalowany w docelowej lokalizacji. Obejmuje to montaż szaf sterowniczych, okablowanie, podłączenie urządzeń peryferyjnych. Kluczowa jest dokładna weryfikacja połączeń elektrycznych. Błędy na tym etapie mogą prowadzić do poważnych awarii.
Po instalacji następuje rozruch systemu. Sprawdza się działanie poszczególnych elementów i całości. Ważne jest przetestowanie wszystkich trybów pracy i sytuacji awaryjnych. Na tym etapie często wprowadza się drobne korekty w oprogramowaniu. Konieczne jest też przeszkolenie operatorów z obsługi nowego systemu. Zwykle trwa to kilka dni i obejmuje teorię oraz ćwiczenia praktyczne. Dobrze przeprowadzony rozruch zwiększa niezawodność systemu w późniejszej eksploatacji.
Sterowniki programowalne wymagają regularnej konserwacji. Obejmuje ona czyszczenie, kontrolę połączeń, aktualizacje oprogramowania. Typowo przeprowadza się ją co 6-12 miesięcy. Ważne jest też monitorowanie parametrów pracy sterownika, jak temperatura czy obciążenie CPU. Pozwala to wykryć potencjalne problemy, zanim doprowadzą do awarii. W przypadku bardziej złożonych systemów warto rozważyć zdalny monitoring. Umożliwia on szybką reakcję serwisu w razie nieprawidłowości.
Przy utrzymaniu systemów automatyki kluczowe jest zarządzanie zmianami. Każda modyfikacja powinna być starannie zaplanowana i przetestowana. Należy aktualizować dokumentację techniczną po wprowadzeniu zmian. Ważne jest też tworzenie kopii zapasowych programów sterowników. Pozwala to szybko przywrócić system do działania w razie awarii. Dobrą praktyką jest prowadzenie dziennika zdarzeń i wykonanych prac. Ułatwia to diagnozowanie problemów i planowanie konserwacji. Profesjonalne utrzymanie ruchu znacząco zwiększa dostępność i niezawodność systemów automatyki.